As a pattern-maker, textile printer and natural dyer – Sarah Burns is passionate about slow, local production that creates beautiful fabric and is kind to our environment. We’re excited to have Sarah in the Handprinted Studio teaching Block Printing with Natural Dyes on Wednesday 20th and Wednesday 27th November 2019.
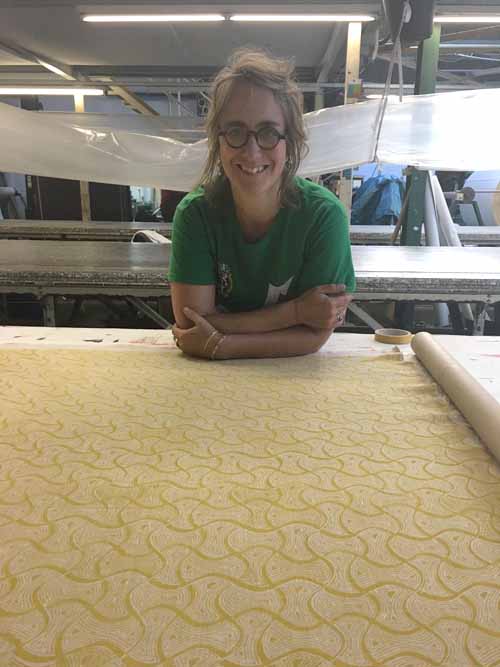
Describe your printmaking process.
I start with an initial idea and cut my block very soon as printmaking is an integral part of designing for me. I’ll keep printing and cutting and changing the block, editing the idea as it develops and being attentive to detail, colour, marks & scale… My goal is to create something that creates both harmony & movement – at the same time.
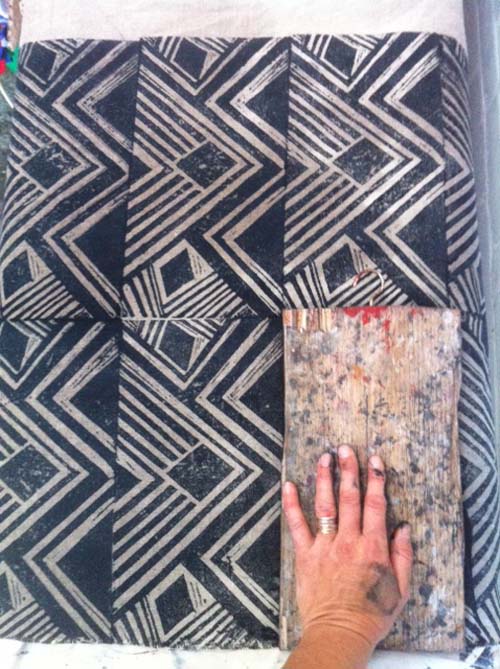
How and where did you learn to print?
Although I went to Cambridge and studied politics, I had a lovely friend who was at art school and we used to block print together – after that I never really stopped even though I was working in a very different field (community economics where I met my husband the writer David Boyle). When I was 40 and my youngest son went to school full time I decided to take the plunge and applied to Chelsea to study textiles – I could cycle there and back to Crystal Palace in time to pick up the kids up. Studying with lots of super talented 20 year olds was terrifying (I was the only mature student) and exhilarating at the same time. I got a first class degree and learned how to work very hard & really shifted in my approach to colour and design.
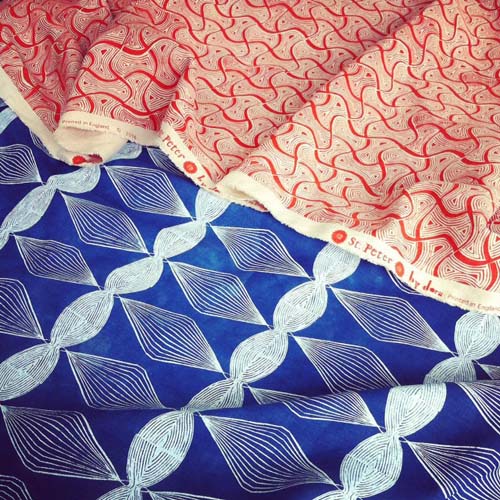
When I was in my second year at Chelsea I started interning with Michal at Christopher Farr Cloth; she took me to the wonderful Ivo’s screen printing factory in Southall and when I graduated I got a job there as a handprinter. I worked at Ivo’s for 3 years, commuting between Sussex and Southall and probably learned more there than I did at college – about colour, technique and the craft of printing. I wasn’t very good at it but it gave me a unique insight into commercial production and English manufacturing. The waste and toxicity of the process also made me want to do things differently so when I set up my studio in Steyning I decided to work in a way that was kinder to the environment – I do believe that beautiful things should be made beautifully otherwise they aren’t really honest.
I’ve just spent two years researching and writing a book on the 1930’s block printers Phyllis Barron & Dorothy Larcher –who combined block printing and natural dyes. Their work has really inspired to work even more with natural processes.
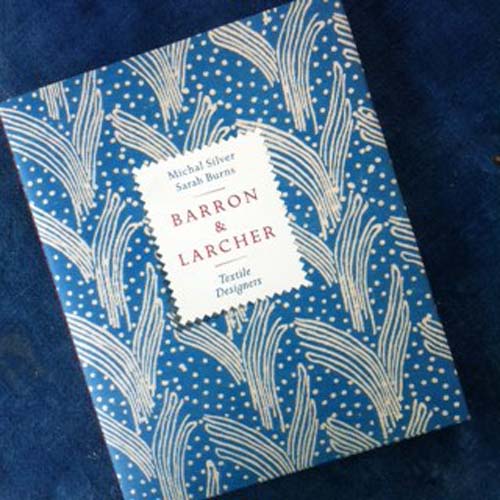
Why printmaking?
I love print because it intervenes between my intention and the final outcome – it always surprises me and acts like an unknown collaborator.
I also love that I am working in reverse – removing the line that I don’t want to print. I’m drawn to resist printing for the same reason.
Colour and pattern is also very important to me – it’s a very emotional and playful thing in my life.
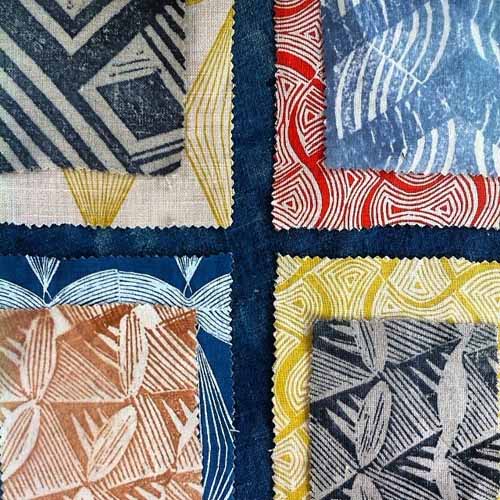
Where do you work?
I now work in my studio workshop cum garage in Steyning West Sussex. I do most of my dyeing outside using whatever plants, fruits or roots are available seasonally and I always have an indigo vat on the go. I also grow lots of dye plants on my allotment and try to get up there most days with my dog Gwennie. Being outside and part of the seasons is very important to me – I try to plant something every day, even if it’s just a handful of seeds thrown into cracks in the pavement.
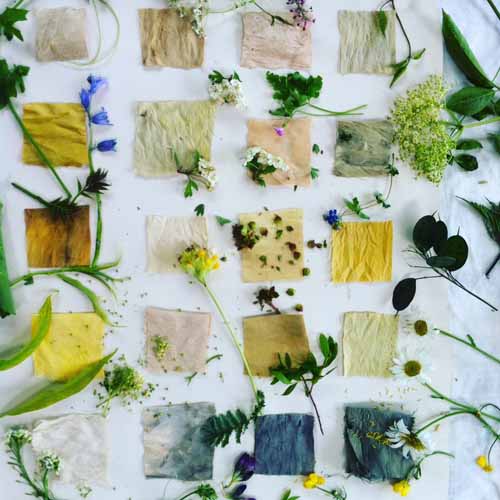
Describe a typical day in your studio.
I’m at my most creative first thing in the morning so I try and get all my blocks, fabric & colour prepped the night before so that I can get up early start printing first thing. The process of dyeing and printing has a definite rhythm to it and it’s one that definitely shapes my days and weeks. I normally print or dye all morning and then get on with other tasks in the afternoon – like preparing orders, organising workshops, talking to clients etc After supper, I often like to cut blocks as they are lovely and soft if you sit on the lino as you eat. In the evenings I’m not good for much excepting getting ready for the next day and maybe doing a bit of website admin. I often find that as I fall asleep problems that have been bugging me all day untangle themselves and new images float into my mind just as I doze off …
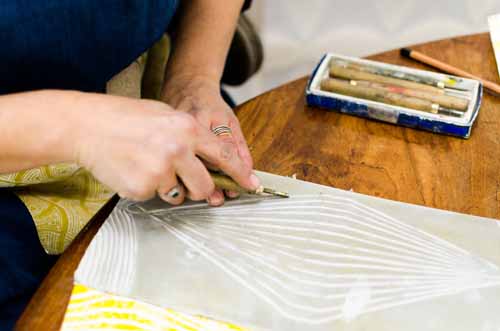
How long have you been printmaking?
For nearly 30 years – it sounds astonishing, especially to me. I’ve had some great teachers – Vivien Lodge at the Working Men’s College in Camden, Kathy Round & Mel Bowles at Chelsea, Podge at Ivo’s in Southall and my children – have all helped me develop in new and better ways. I remember reading somewhere that you don’t master any craft until you’ve put in at least 30,000 – I’m probably reaching the quota now.
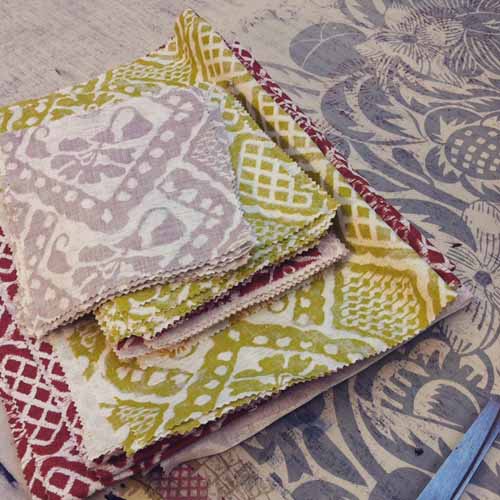
What inspires you?
I’m originally from South Africa and love the traditional shwe shwe cloth or German print that is worn traditionally by domestic servants – I’ve named one of my recent designs Margaret after the lovely woman who looked after me and my brother when we were little. I love vernacular arts and crafts – like the beautiful Romanesque carvings and medieval wall paintings you find in ancient churches around Steyning. Their bold colours and rhythmic patterns are really wonderful. They are very honest and direct, made by incredibly talented and unknown craftsmen. I also like the immediacy and vitality of Peggy Angus for the same reasons. I especially like that she thought about and understood some of the reasons behind pattern making; for me making patterns is full of meaning and emotion and she devoted her life to teaching more people about that.
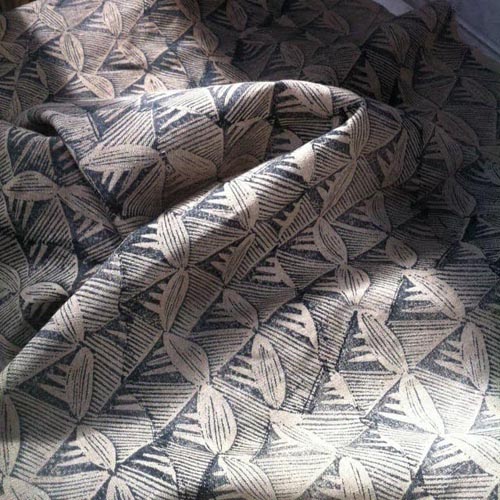
The actual process of patternmaking and printing is what inspires me most – the fabric I begin with, the process of mordanting, preparing the dyes from roots and berries and the act of printmaking itself – at each stage materials change and marks alter, the smells, tastes and feelings – it’s a very sensual process and one I’ve become completely captivated by.
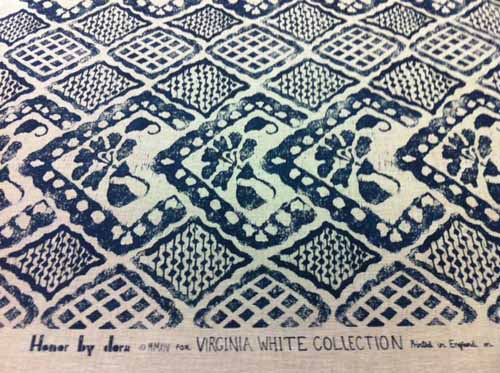
I also love drawing and I mark the beginnings of a holiday by starting to draw as much as I can all the time, every day – I have lots of sketchbooks. When I’m most relaxed I dream about drawing.
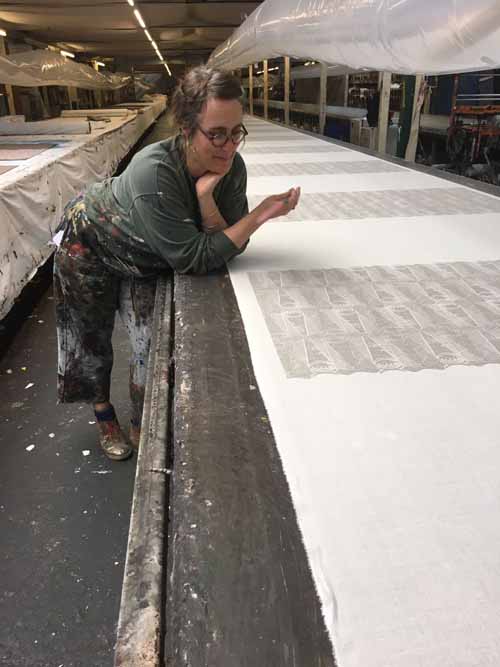
What is your favourite printmaking product?
Probably manutex – because it’s a natural product (made from seaweed) so it’s kind to the environment mixes so well with natural dyes and makes beautiful silky printing paste.
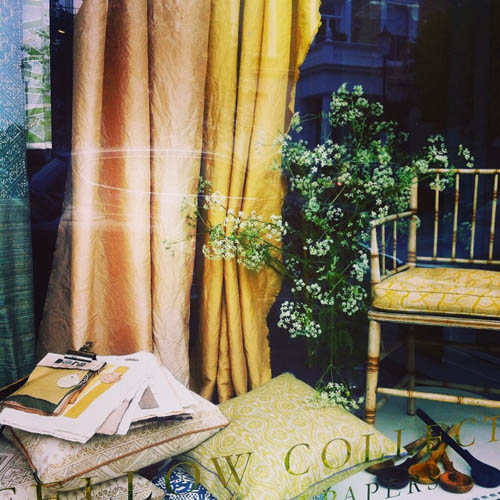
What have you made that you are most proud of?
I spent several years making my map of world patterns – I collected stories from people all around the world and sewed their patterns onto a massive patchwork quilt of the world. The project taught me so much about our relationship to pattern and how patterns travel and change through culture, tradition and people http://unsewn.blogspot.com/2010/
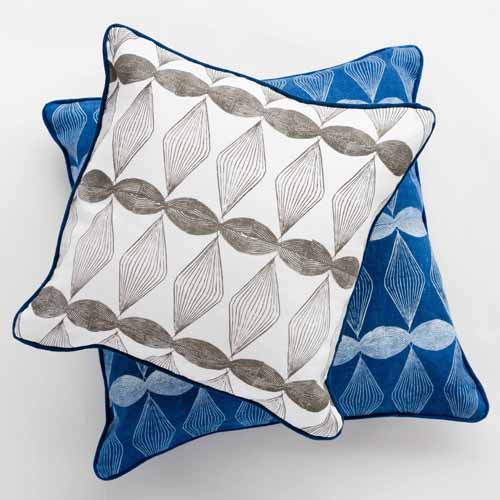
Where can we see your work? Where do you sell?
I sell my naturally dyed and hand block-printed fabrics through my website www.dorafabrics.com
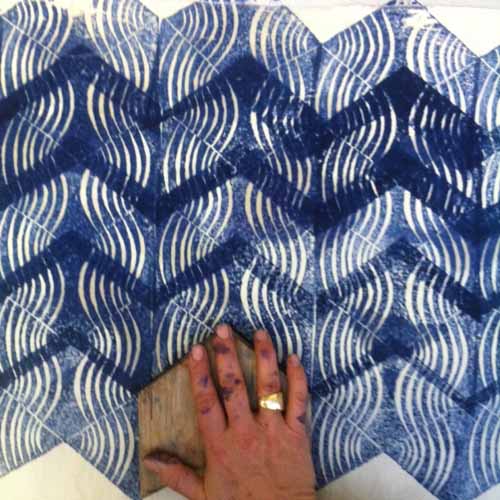
The lovely people at Guy Goodfellow Collection http://www.guygoodfellow.com also keep my work at their showroom in Chelsea. Virginia White has several of my designs in production as part of her fabric and wallpaper collection http://virginiawhitecollection.com/fabrics/ and my friend Alice Garner and I run the Steyning Imprint together – making tea towels and other lovely things for sale through our Etsy shop http://www.etsy.com/uk/shop/steyningimprint
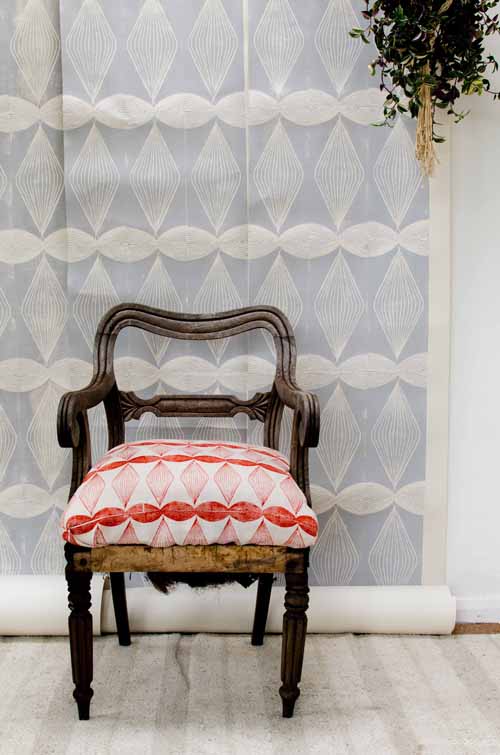
What will we be seeing from you next?
I’m really excited to be out and about with my Barron and Larcher book this year – and I’ve been involved in helping with the Women’s Work show at Ditchling which celebrates craftswomen who turned their practice’s into successful businesses between the two World Wars – including Ethel Mairet, Alice Hindson, Phyllis Barron & Dorothy Larcher, Enid Marx, Catherine ‘Casty’ Cobb, Katharine Pleydell- Bouverie, Denise Wren and Elizabeth Peacock.
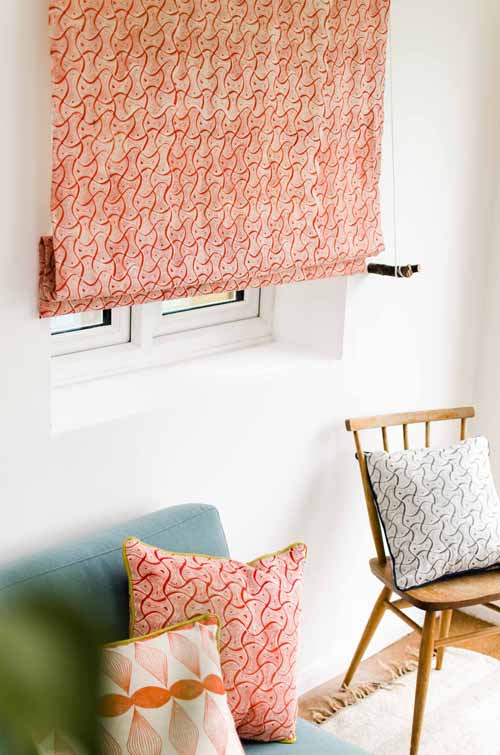
My partner Alice and I will be doing a Barron & Larcher inspired workshop there in June. I’m really excited to be following in their footsteps – pioneering low-tech, non-toxic textile making.
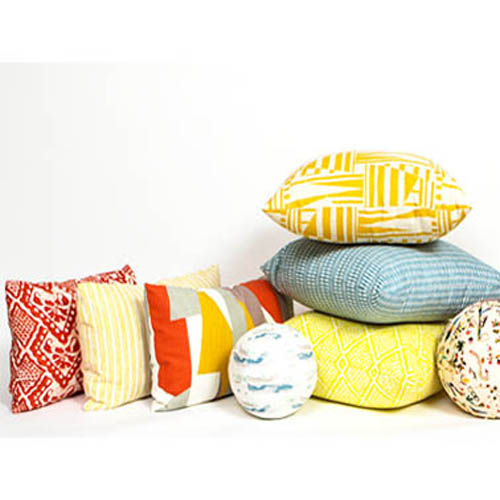
Do you have any advice for other printmakers and creatives?
Follow your passion and be brave.
Work hard and keep going – stamina is just as important as talent.
Try and learn something from everyone you meet – everyone has something to teach you.
Find good people to work with – the ideas you have together will nearly always be better than thoughts you have alone and they will be there to keep you going when you run out of steam.
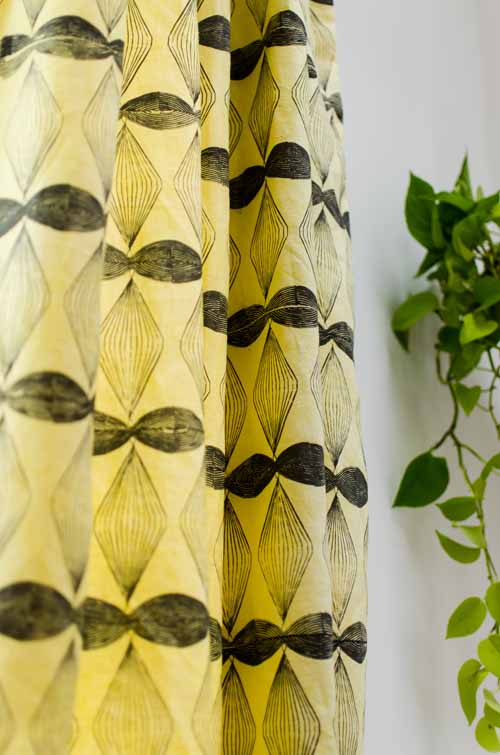
Instagram: @patternmakers