
I’m really a linocut hobbiest, artist and enthusiast. I enjoy spending my spare time carving into a piece of lino as my creative outlet. When I started
I had lots of questions, and I wanted to share my knowledge and experience to help and encourage others. I decided to setup Draw Cut Ink Press, my website, to document my journey and to act as an online resource to encourage others to pick up the tools
and start linocutting and printing.
I started off my career as a freelance illustrator and graphic designer before working with my business partner to setup a digital agency which makes up
my day job. As the agency has grown I found myself further away from the creative coal face and so wanted a past-time that scratched my creative itch.
I love every part of the linocutting and printing art form, from the process of planning and carving the piece to inking up my latest block and peeling
back the paper for the first time to reveal how the lino print turned out.

Describe your process.
I always begin with a pencil and an idea. I have lots and lots of ideas all the time so I keep a notebook on me where I can jot down any new creative sparks
of inspiration and slowly try to work through them all.
I like to draw directly onto a piece of lino, and once I’ve sketched my initial plan out I’ll then begin to add areas of light and dark with a black brush
pen. This really helps get the composition ready and allows me to map it out before I start carving away the negative space.
I use a set of Pfeil carving tools to cut away the lino and add areas of shading. I really enjoy experimenting with the variety of marks you can create by combining different techniques
and U shaped or V shaped tools. I think that this is the part of the process I enjoy the most. I find it really relaxing, it’s almost a type of therapy
and hours can just evaporate!
Once the process of cutting away the lino is complete, I’m pretty much ready to get printing. If I’m doing a multiple colour block then the process is
a little bit more complicated, as you have to map out the areas where you want to add some extra colour and create a registration template (I’ve written an article about that on my blog).
I have a book press at home, but I like to use an etching press most of the time when I’m printing. Using oil based relief printing inks and a Japanese
roller I’ll ink up the lino. Then I’ll crank it through the etching press and hey presto, the job is done and I’m straight back to my notebook to see
what the next print will be from my list.

How and where did you learn lino printing?
I just started doing it really, which means I made loads of mistakes! This was why I wanted to setup Draw Cut Ink Press,
in order to document what I’d learnt and to make it accessible and free to anybody else who is interested. The only training I’ve done was with Nick
Morely (aka LinocutBoy) at Resort Studios in Margate. My wife got me a weekend colour workshop
where I learned loads from Nick, who is a top print artist and really nice bloke.
Do you practice any other forms of printmaking?
I’ve done some screen printing before, and I’d like to try wood block printing one day but at the moment I’m really just focused on lino printing.

Where do you print?
I have a membership for Bainbridge Studios in Elephant and Castle in London. The studio is primarily setup for screen printers, but they’ve also got a
little back room with two etching presses that seem to mostly collect dust. I’m very pleased to dust them down and run my blocks through them, I think
they are fantastic.
Describe a typical day when you are printmaking?
I have two typical types of day really. Drawing and carving at home, or printing in the studio. I’ll usually stick some music on (I’d always recommend
The Rolling Stones) and just bury myself into what ever part of the process I’m at. When I’m carving the lino I tend to work in the evenings or for
a few hours at the weekend. When I’m printing I’ll book a four hour slot on the etching press at the studio and try to work through as quickly as I
can, especially if I’m doing a multi-block print.
How long have you been printmaking?
I’ve been printing for just over a year now, and I’m sure that I’ll be printing for many years to come. I hope!
What inspires you?
Lots of things, I have a really eclectic taste when it comes to things that I find inspiring. The first block print that really inspired me was an Ex-Libris
print a friend bought on a visit to Prague. I loved the graphic quality of it, and I’ve since found loads of these that get my creative juices flowing.
I love popular culture, from great musicians to cult movies as well as the just the world around me, from the city I live in to nature and big landscapes.
I think that if I had to express one thing that ties all my work together it is a sense of narrative and story telling, I like all my prints to look and
feel like a snap shot of an unfolding story.
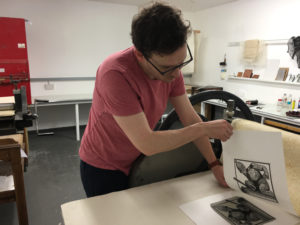
What is your favourite printmaking product?
That’s a tricky question to answer, but I think my set of Pfeil carving tools are my absolute favourites. I can’t live without them now. When I started lino cutting I had a naff carving
tool with a blunt cutting edge and cheap plastic handle. It was so bad I almost packed it in before I’d had a chance to start, but then I decided to
invest some pennies into my first Pfeil tools and it was a completely different experience, I loved it!
What have you made that you are most proud of?
Another tough question, I think that as a creative person you always look at the flaws in what you’ve done because you’re too close to the pieces you create.
I’ve done a few pieces that I like, but I only start really liking them about two months after they’re printed and have sat under a pile on my desk
for a while.
I think some of my recent work is what I like the most, which have been based on characters from films I grew up with. I loved the old movies that merged
stop motion animation with live action, and so my latest piece of the mythological Greek character Talos that came to life in Jason and the Argonauts
is currently my favourite.

Where can we see your work? Where do you sell?
Primarily on my website or my Instagram feed at the moment. I have plans to eventually start selling my work via my website and to maybe try and exhibit in a few small galleries in London
if I have the opportunity.
A few people contact me through social media so I’ve made a couple of sales, but for me lino printing is primarily a hobby. The dream is to one day setup
my own studio and surround myself with other artists all day – to create a bit of a lino cutting and printing community where we can support one another
and setup classes, workshops and exhibitions open to people interested in the art form.
What are you working on at the moment?
Right now I’m doing a series around my stop-motion animation childhood hero Ray Harryhausen and the characters that he created. I want to try and get around
ten pieces in the series, so I’ve got a way to go yet!! The latest piece hot off the press is of Talos, a giant bronze statue that comes to life in
Jason and The Argonauts, but as I write this I’m looking for skeleton warrior references (as you do??) from the same movie…

Do you have any advice for other printmakers, designers and creatives?
I’d say just get on with it really, you can start lino-printing at home with relatively few tools and you don’t need loads of space. The most important
thing is to just be open to experimentation and the odd failure along the road. Mistakes are the best way to learn and I’ve certainly learnt the most
by making a few clangers along the way. Art is really 1% inspiration and 99% perspiration, so be prepared to roll your sleeves up and sweat it out.
It’ll definitely be worth it in the end.
The only other advise would be to look at what other people are doing if you don’t know where to start. There are loads of inspiring people doing amazing
work out there, and I’m sure that one of them will be able to inspire you to get printing too… and obviously i’d say to go and have a look at
www.drawcutinkpress.com for lots of helpful articles and tips!
You can see more of Paul Davis’s work on his website, on Twitter or Instagram!Â